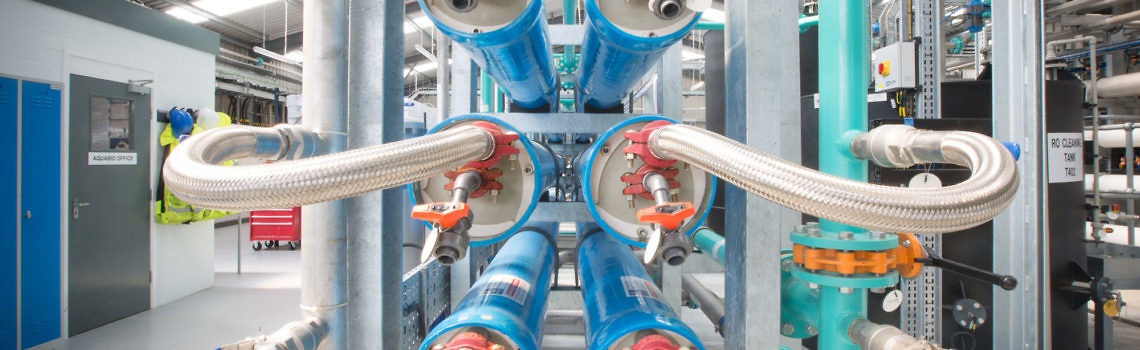
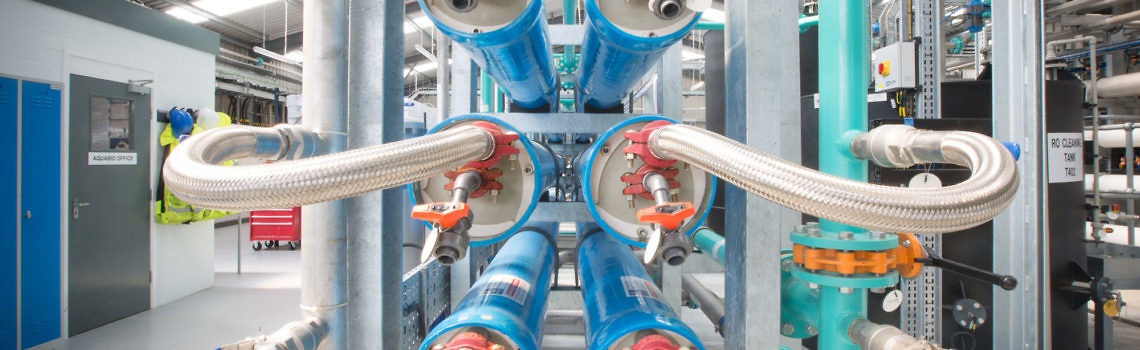
Reverse Osmosis
Working in conjunction with our AMBR or AMBR LE technologies, Aquabio’s conventional RO and novel ROne™ plants provide demineralised water which can be used in the following reuse applications:
- Demineralised water reuse as boiler feed water
- Reuse for CIP applications
- Potable water reuse for food washing
- Potable water reuse for complete factory water supplies
Further combined with UV technology, exceptional quality water is achieved which complies with the UK’s Private Water Supply Regulations 2016, to allow potable water reuse for food contact and human consumption.
Aquabio’s RO units focus on ease of operation due to a high degree of automation together with ease of maintenance. A permanent cleaning system is provided including all required valves and pipework, to minimise down time during offline cleans. Depending on the requirements, additional pH control, remineralisation, temperature adjustment or residual disinfectant treatment may be included.
Aquabio provides 2 types of RO systems, of which each is carefully designed and selected to best meet with the client’s needs and processes.
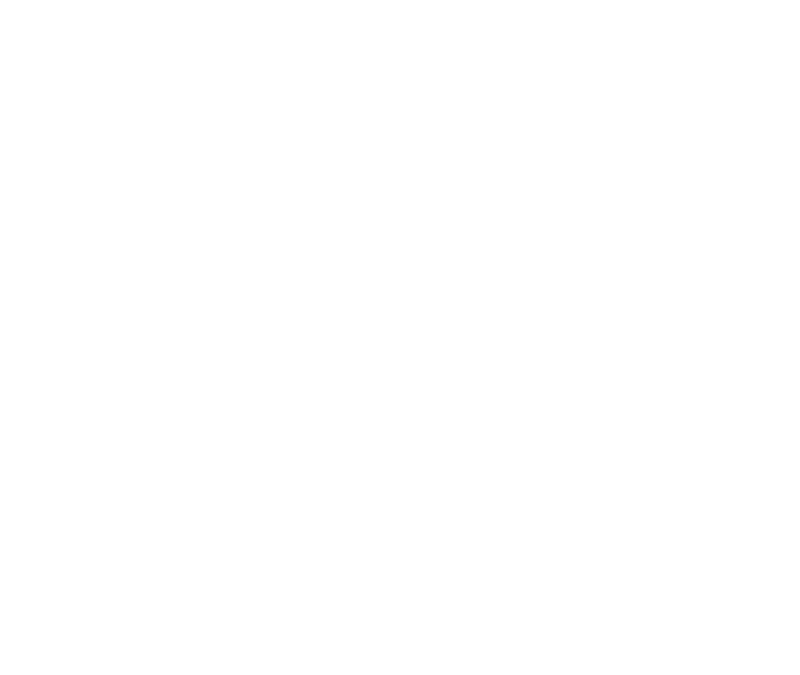
ROne™
Aquabio’s ROne™ system has been developed in recent years to provide a wholly flexible operation compared with conventional RO system configurations.
By incorporating a variable speed RO Reject Recirculation Pump, a proportion of the RO Reject (concentrated stream) is recirculated through the ROne system to achieve water recovery of up to 95%, compared with typically up to 75% recovery on a conventional RO plant.
The ROne novel configuration overcomes the limitations of conventional RO systems enabling the system to operate at variable feed flows and therefore is adaptable to changing process conditions. This enables greater or lesser recovery as required (turndown capacity), optimising energy usage, and also prevents unnecessary on/off cycles, providing a continuous stable operation and minimum downtime.
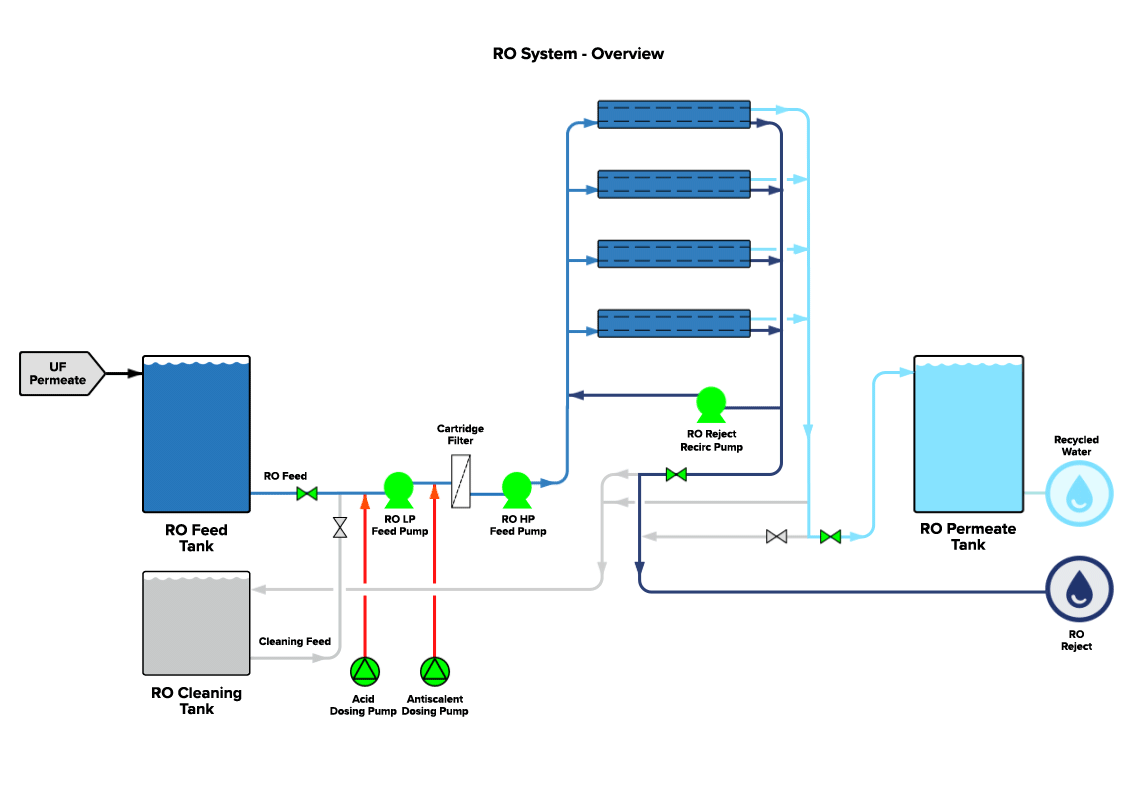
Conventional RO
Aquabio’s conventional RO system provides the backbone to the new ROne™, and has been utilised as part of Aquabio’s water reuse solutions since Aquabio’s first water reuse installation in 2001.
With the conventional RO configuration, the concentrate from the first stage of the RO system becomes the feed to the second stage, commonly referred as ‘concentrate staging’. As permeate is produced in Stage 1, a pyramid configuration of pressure vessels is commonly used to maintain a similar feed flow rate in all vessels of the system, and to maintain the concentrate flow rate per vessel above the required lower limits.
The conventional RO system configuration and operating parameters such as number of vessels/elements, number of stages, recovery in each stage, system feed flow and total recovery are carefully defined during the design phase of the RO system.
Aquabio’s conventional RO plant is suitable for applications which require a higher quality RO permeate, a lower degree of permeate recovery and/or flexibility in operation (turndown capacity) or where a lower CAPEX is a consideration.
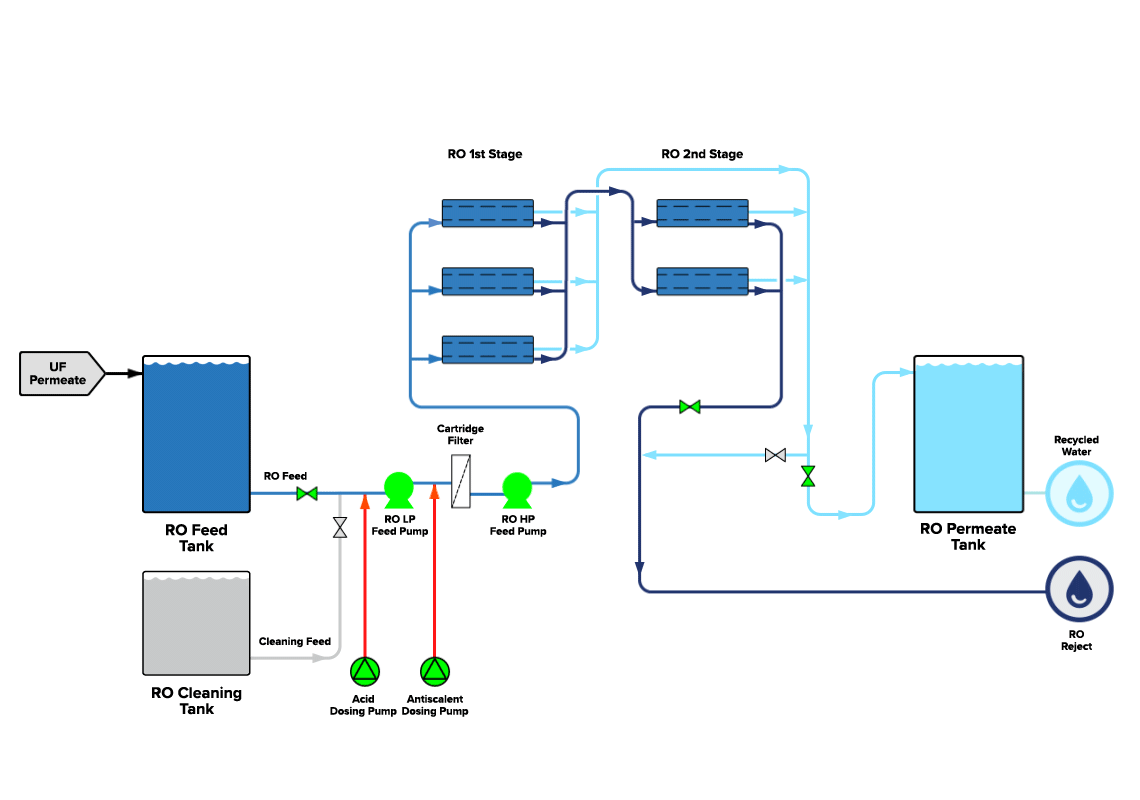
Key Features/Benefits | CONVENTIONAL RO | ROne |
---|---|---|
Compact design | ✓ | ✓ |
Low fouling membrane modules allow for low pressure / low energy operation | ✓ | ✓ |
Variable speed control to reduce energy usage | ✓ | ✓ |
Automated 'ramp' up & down capability to deal with varying throughput | ✗ | ✓ |
Maintained % recovery | ✗ | ✓ |
Adaptable to changing process conditions (greater or lesser recovery) | ✗ | ✓ |
Adaptable to upstream & downstream processes to prevent unnecessary on/off cycles | ✗ | ✓ |
Modular design enables easy upgrade with additional modules or banks for increase in capacity | ✓ | ✓ |
Standardised RO skid - rapid procurement and installation | ✓ | ✓ |
Ease of integration with upstream and downstream equipment | ✓ | ✓ |
Option of containerised installation | ✓ | ✓ |
Advanced pretested, standardized software and control system | ✓ | ✓ |
Protective control for key parameters | ✓ | ✓ |
Robust, proven, best available technology | ✓ | ✓ |
Conforms to requirements of UK Private Water Supply Regulation 2016 and equivalent international standards | ✓ | ✓ |